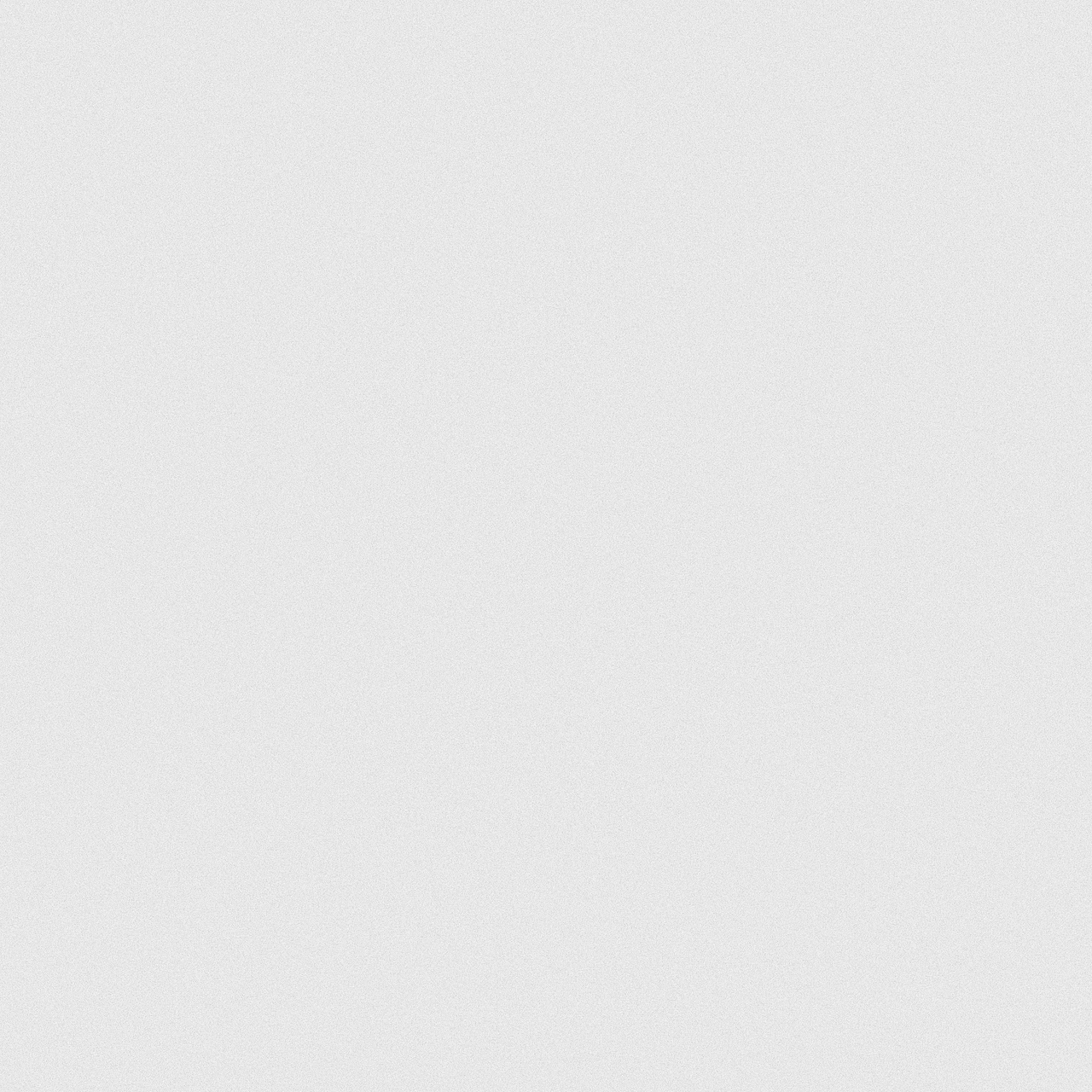
Pyrometers & Infrared Thermometer
EEC is an established name in supplying of all types of Pyrometer and infrared thermometer. We offer complete range of pyrometers and infrared thermometers to suit different industrial applications.

Pyrometers
Pyrometers are temperature measurement instruments that operate on the principle of infrared radiation, i.e. they detect infrared radiation of objects to determine the temperature.
An optical pyrometer determines the temperature of a very hot object by the color of the visible light it gives off. The color of the light can be determined by comparing it with the color of an electrically heated metal wire. In one type of pyrometer, the temperature of the wire is varied by varying the strength of the current until the operator of the instrument determines that the color of the wire matches the color of the object. A dial, operated by the current that heats the wire, indicates the temperature.
A radiation pyrometer determines the temperature of an object from the radiation (infrared and, if present, visible light) given off by the object. The radiation is directed at a heat-sensitive element such as a thermocouple, a device that produces an electric current when part of it is heated. The hotter the object, the more current is generated by the thermocouple. The current operates a dial that indicates temperature.
With a huge pyrometer product portfolio, we provide solutions for nearly every application request. Special solutions that are not listed below can also be quickly adapted to customer or application specific specifications.
Categorization:
-
Pyrometers for predominantly non-metallic surfaces
-
Pyrometers for metallic surfaces, ceramics, graphite
-
Pyrometers for glass surfaces
-
Pyrometers for special materials
Applications:
Infrared Temperature Measurement in Steel Processing
Noncontact infrared thermometers in steel manufacturing process where temperature monitoring is critical to productivity and product quality. Every section of the steel manufacturing can benefit from temperature monitoring.
Raw Materials for Steel Production
Monitoring temperatures of iron ore, lime, coal and coke insures that the basic raw materials have achieved the right characteristics and prevents critical conveyor belts from being damaged. Continuous scans of stove dome temperatures are a requirement for maintaining correct operation of the blast furnace.
Steelmaking – Blast Furnace
Stove dome: Thermal scans prevent overheating and premature damage to the refractory bricks.
Molten iron: Temperature monitoring during tapping ensures continuous feedback and product uniformity.
Torpedo car: Linescanning finds refractory failures and avoids costly and dangerous metal spills.
Continuous Casting
Using infrared thermometers accurately gauge cooling requirements of slabs, billets, or blooms to ensure product uniformity throughout, and provide equipment operators with immediate temperature information vital to the cooling process.
Rolling Mills
Infrared temperature sensors accurately measure strip and sheet temperature so that rolling mill stands can be efficiently set to match the steel’s temperature. IR sensors can also be used to detect the presence of hot metal to accurately time roll stand operation.
Tube/Pipe Mills
Welded tube relies on accurate measurement of weld seem temperatures to insure 100% integrity of the seal and prevent bad or low quality tube. Monitoring the billet temperature in pipe mills allows the operator to adjust rollers, which results in reduced process downtime.
Rod/Wire Mills
Thermal scans of billet exit temperatures allow the operator to adjust rollers and reduce process downtime. Sensors mounted at the layering area control cooling of overlapping coils to improve product quality.
Heat Treating
Ratio IR thermometers allow accurate temperature measurement of parts often obscured by smoke, steam, and quench oil in an EMI environment. Factory operators can selectively control temperature measurement of heat treated parts, resulting in significant energy and time savings.
Steel Coating
Sheet temperatures can be monitored before and after coating to insure the coating will bond and have the desired thickness.
Forging
Infrared sensors measure work-piece temperatures without interfering with the process to insure that correct metallurgical properties, such as grain size and structure are achieved. Monitoring temperature reduces heating costs by preventing billet overheating and reduces machine and die maintenance by identifying under heated billets before working.
Infrared Temperature Measurement in Glass Processing
Noncontact infrared thermometers are designed for use in glass industries where monitoring and controlling temperature is critical to productivity and product quality. IR sensors are used with furnaces, bulk glass, melter, regenerator, refiner, forehearth, gob, molds, float lines, and annealing lehrs, as well as at the cooling and coating areas.
Melt Furnace
Regenerators improve fuel efficiency by heating incoming air and alternating the firing direction. To insure maximum operating efficiency, noncontact IR sensors are mounted at the top and bottom of each regenerator to trigger the air flow and firing direction at the optimum time. Monitoring the packing and refractory material for deterioration is crucial in planning the maintenance and rebuilding schedules, and eliminating emergency situations which could cause a costly, unscheduled shut down.
Flat Glass
Temperature monitoring is critical in each stage of flat glass production. Incorrect temperatures or rapid temperature changes cause uneven expansion and contraction, resulting in improper annealing. Noncontact sensors are mounted at the tin bath and annealing lehr to insure correct glass temperature.
Bottles and Containers
Infrared fiber optic sensors are placed along the forehearth to monitor the proper molten glass homogenous condition at exit and control the forehearth zone temperatures. Sensors mounted over each of the annealing lehr’s temperature zones can accurately monitor and control the cooling process and cold end surface treatment.
Glass Fiber
Use infrared fiber optic sensors to monitor and control forehearth zone temperatures to maintain the optimum molten glass temperature as it enters the fiberizer.
Infrared Temperature Measurement in Paper Processing, Packaging and Converting
Noncontact infrared thermometers are used in many steps of paper production and processing where temperature monitoring is critical to productivity and product quality.
Process Imaging and Monitoring System for Extrusion Coating and Laminating
The Extrusion Coating System is an automated surface inspection system that detects wavy or torn edges, monitors width, and insures proper web temperatures for strong film-to-substrate adhesion in plastic film extrusion processes. Temperature data can be saved as a graph or thermal image and printed or saved for future analysis. Early detection of imperfections improves product quality and increases profitability by reducing scrap.
Web Process Imaging System
The Sheet Extrusion System monitors the temperature distribution of moving webs in the manufacture of paper and plastic, as well as a broad range of other industrial applications.
Infrared Temperature Measurement in Plastic Processing
We offer a wide variety of infrared thermometers that monitor and control temperature in plastics manufacturing processes. These industrial temperature sensors monitor fast moving processes quickly and efficiently. They measure the temperature of the product directly, instead of the oven or the dryer, allowing you to quickly adjust process parameters to ensure top product quality.
Industrial infrared thermal imaging systems are easily integrated into existing process control systems and have the following benefits:
-
Non-destructive: the product is never touched or contaminated.
-
Fast and reliable: moving objects are measured accurately and quickly.
-
Flexible: temperature measurements can be made of a large area or a small spot.
Infrared Temperature Measurement in Solar Equipment Manufacturing
Infrared thermometers are designed for use in the solar industry, where monitoring and controlling temperature is critical to productivity and product quality. From silicon and wafer production to photo voltaic cell and module manufacturing, we have the products needed at every step of your online process monitoring – even in hazardous and potentially explosive environments, such as hydrogen reduction processes.
Polysilicon Production (Siemens Process)
Efficient temperature measurement is important in controlling the heating of silicon rods inside a Siemens process CVD reactor. Measurement of the byproduct Silicon tetrachloride (STC) process when it is recycled and converted into Trichlorosilane (TCS) for reuse is also necessary. High performance infrared thermometers with variable focus, high resolution optics are needed to properly target the polysilicon rods and not be affected by the process environment or from the build-up of contamination on process reactor windows. Special explosion proof enclosures are also needed during hydrogen reduction processes.
Single Crystal Silicon Production (Czochralski Process)
Proper temperature measurement of the silicon liquid used in the crystal pulling process for single crystal manufacturing helps insure wafer quality. High performance infrared thermometers with variable focus and high resolution optics provide the small measurement spot required to precisely measure the silicon liquid/solid freeze point and properly control the crystal pulling process. Silicon melt and crucible temperatures can also be monitored and controlled.
Thin Film Deposition (PV Modules)
Measuring the temperature distribution of the film deposition and the substrate of the solar panel is critical in this process. A high resolution thermal image of the entire panel surface allows proper tuning of the ovens used in the deposition process (sputtering, printing). Non-uniform temperature profiles or incorrect process temperatures can lead to voids and poor PV module performance and failure.
Thermal imaging can also be used to identify cracked or broken solar cells, as well as defects in the electrical connections caused by poor solder joints.
Infrared Temperature Measurement in Building and Construction Materials Manufacturing
Infrared Imaging Systems and Fixed Thermal Imagers are used in many steps of building materials manufacturing starting with cement processing, to wallboard and pressboard manufacturing, as well as architectural glass production and tempering, where monitoring and controlling temperature is critical to productivity and product quality.
Cement Processing
Infrared Monitoring of Kiln Shells Extends Refractory Life. Extending the life of kiln refractory and preventing disastrous failures requires a good understanding of the condition of the refractory material. The easiest way to monitor the gradual refractory degradation and to detect damaged or fallen bricks is to monitor the temperature of the kiln shell. Infrared technology provides perfect solutions to perform this task and sophisticated, user-friendly interfaces make it easy to analyze and understand the data.
Thermal Imaging and Profiling System for Wallboard & Pressboard Applications
Thermal Imaging System measures wallboard moisture content, identifies board defects, and simplifies dryer process monitoring and control. The real-time board map displays a detailed image of each board set as it leaves the dryer, providing comprehensive board moisture and quality information.
Construction Glass Manufacturing and Tempering
Thermal Imaging System is an automated temperature measurement system for glass bending, forming, annealing, and tempering processes. It also works for Low Emissivity (Low-E) glass with automatic emissivity correction, designed to monitor manufacturing of one-side coated construction flat glass.
Benefits:
-
Automated process control
-
Improved Quality
-
Increased product uniformity
-
Reduced production costs and downtime
Our pyrometers & infrared thermometer portfolio includes world class brands like:
-
LumaSense / IMPAC
-
Raytek
-
IRCON
-
Tempsens
-
Sensotherm
-
DIAS
-
HTC
-
Fluke
Note: Most of the models are readily available with us and we have the expertise to suggest pin to pin equivalent in alternate brands as per customer’s need.